Welding Design
WELDNG CALCULATOR
WELDABILITY
The weldability also known as joinability of a material refers to its ability of welding. Many metals and thermoplastics can be welded, but some are easily welded than others. A material's weldability is used to determine the welding process and to compare the final weld quality with other materials.
A build in calculator can help user to calculate many useful results, which can be used for weldability analysis.
The Welding Calculator supports the planning and optimization of welding tasks such as the calculation of weldability, cooling time, preheating temperature and the required filler metal quantities.
- CE, NiEQ, CrEQ
- PCM, CEN, HCS, Reheat crack
- Phase balance, FNA
- Cooling time t8/5
- Pre-heat temperature
- AC1, AC3, MS temperature
- HAZ hardness, tensile strength etc.
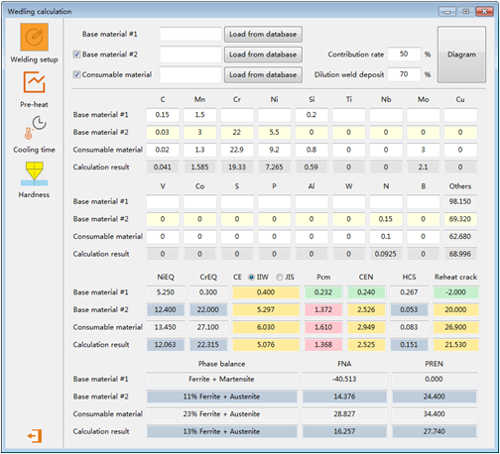
Weld calculator interface
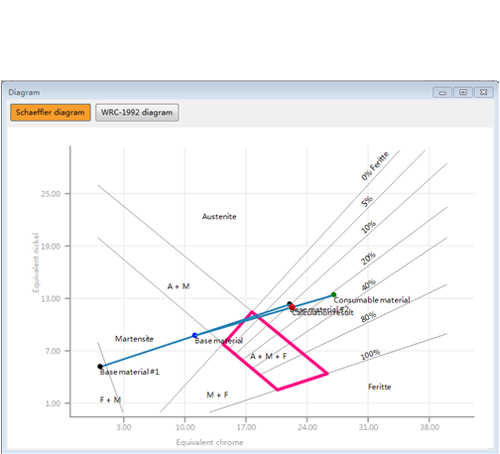
Schaeffler diagram
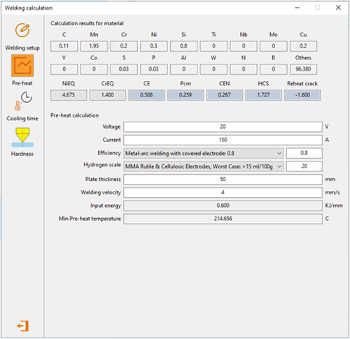
Pre-heat calculator
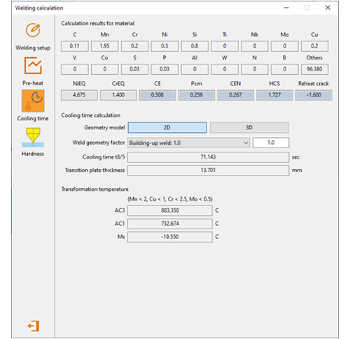
Cooling time t8/5
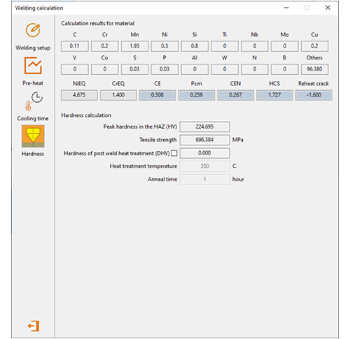
HAZ hardness calculator
SMARTWELD OPTIMIZATION TOOLS
The SmartWeld optimization and analysis tools have been developed to do weld analysis and provide optimal weld schedules for CO2 continuous wave laser welding, pulsed Nd: YAG laser welding, and for non-consumable arc welding process.
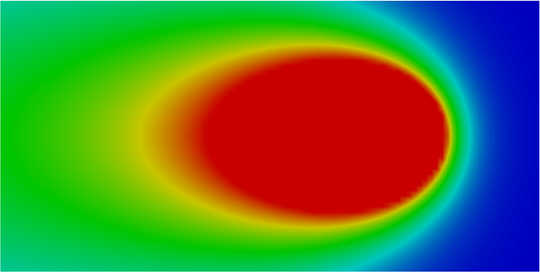
- Input power (watts): 2980
- Welding speed (mm/sec): 5.3
- Width of weld (mm): 6.74
- Penetration depth (mm): 3.37
- Melt efficiency: 0.299
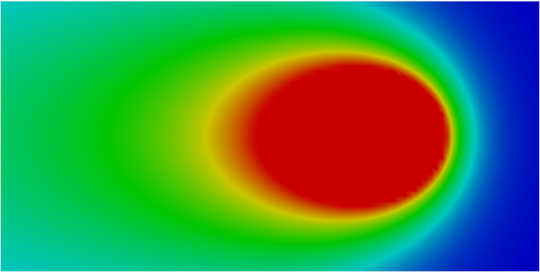
- Input power (watts): 2240
- Welding speed (mm/sec): 4.2
- Width of weld (mm): 6.22
- Penetration depth (mm): 3.11
- Melt efficiency: 0.268
Two Primary Uses FOR SMARTWELD
Predictive
- Science based process models enable optimized automated weld procedures.
- Virtual manufacturing enables the user to ask “what if ?” and quickly find the answer.
- With SmartWeld, multiple welds do not need to be made in order to determine weld effects and required parameters.
Investigative
- Welding problems can be solved by gathering information on efficiencies and other figures of merit.
- Most SmartWeld models are universal and can be applied to many different weld processes.
- Understand your welding process better.
- The optimization methodology consists of mixed genetic and gradient-base algorithms to query semi-empirical and nonlinear algebraic models.
- The optimization output provides heat-input-efficient welds for user-specified weld dimensions.
- User querying of all weld models is available to examine sub-optimal schedules.
WELD PROCESSES
- ARC Weld: Compute an optimal procedure for thin/thick plate
- OSLW: Compute an optimal continue wave laser weld procedure
- Nd: YAG: Compute an optimal pulse Nd: YAG weld procedure
- SPOT-3D: Compute an optimal thick plate spot weld procedure
- HAZ-CYCLE: Compute temperature history in the heat affected zone.
SMARTWELD RESULTS
- Temperatures surrounding the weld (maximum and history)
- Weld size (width, depth, cross section area)
- Effect of material type
- Process parameter values
- Efficiencies
- Effect of metal thickness
- Procedure sensitivities
- Parameters optimization
- What if?
MATERIAL DATA IN SMARTWELD
- 304 stainless, 18Cr-8Ni stainless steel
- 15-5PH stainless steel
- 17Cr-4Ni martensitic stainless steel
- 1018 steel
- HY130 – 0.12C-5Ni-0.6Cr-0.5Mo steel
- HY80 -0.18C-2.6Ni-1.4Cr-0.4Mo steel
- Tin / Molybdenum
- Nickel 200
- Kovar – 29Ni-17Co low expansion alloy
- 1100 aluminum / 6061 aluminum
- 110 copper
- Hastelloy C4 – Ni-16Cr-16Mo alloy
- Hastelloy C22 – Ni-22Cr-12Mo-3W-3Fe
- Hastelloy B2 – Ni-28Mo
- Inconel 718 / Inconel 625
- Ti-6Al-4V: Titanium alloy for aerospace