Stress & Distortion Analysis
The Cast-Designer can perform the full couple simulation of thermal, flow and stress together. The stress simulation includes both thermal and mechanical stress, which accurately predicts casting residual stresses and distortion.
Stress Results
- Distortion / Displacement
- Compensation for Distortion
- Normal Stress
- Effective Stress
- Strain
- Fatigue
- Hot Tearing(...)
In addition, with the stress module, the user can achieve the following goals:
- Casting and mould stress & strain distribution
- Part deformation and distortion
- Gap formation between the casting and mould
- Predict elastic spring back
- Hot tearing and cracking indication
- Die life fatigue
Cast-Designer stress module helps casting part designers and die designers to consistently predict the dimensions of a casting part after cooling, with being able to closely predict casting dimensions will lead to
- Better Design: Helps designer to make a better casting part design
- Better Die Design: Helps die designers to compensate for the part distortion during the die design stage. Thus, reduce the rate of scrapped castings
- Quality Improvement: Being able to closely predict casting dimensions will lead to tighter tolerance and thinner walls results in high quality castings and reduced scrap
- Save Time: Saves development time
- Save Cost: Reduces operation cost due to improved first shot capabilities and fewer number of interruptions
- Improved Efficiency: Better products with reduced cost help to redefine competitiveness
- In Cast-Designer, A new Distortion Compensation Solver (DCS) was developed based on the mechanical stress solver to find compensation geometry automatically.
- In DCS, user can select a set of Sensor points/ Critical points, where user wants to control the distortion.
- It is an iteration method to find the best geometry shape to avoid the distortion in the casting and the importance is given to the selected sensor points in the final casting.
- Finally, the adjustment distance of feature points is reported and can be used in the CAD system. It is a unique product in the industry.
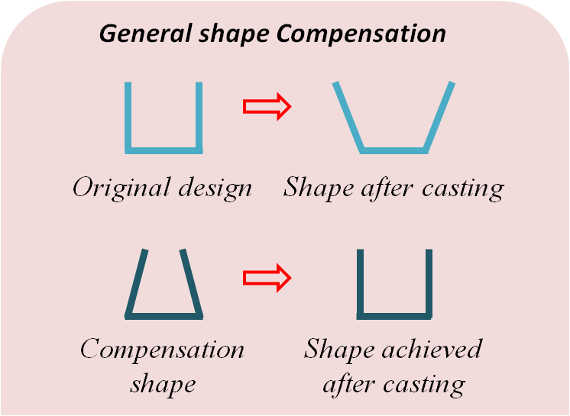
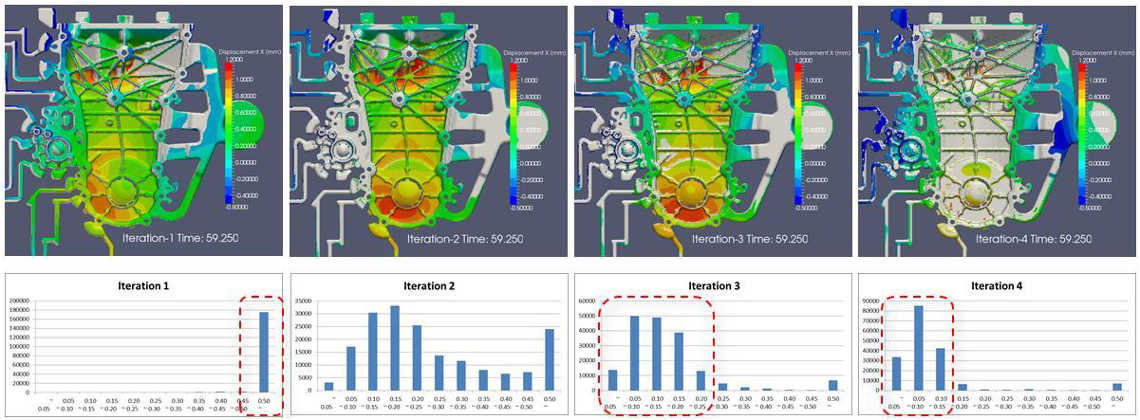
After the first iteration, the amount of deformation exceeded the tolerance and reached above 0.8mm. The flatness requirement of the product was 0.5mm. After four automatic iterations the product flatness is maintained between 0.05 and 0.15, and the product 100% meets the requirement.
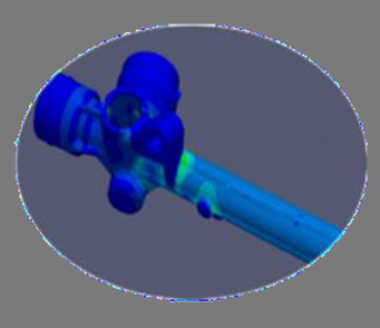
Hot-tearing indicated in simulation
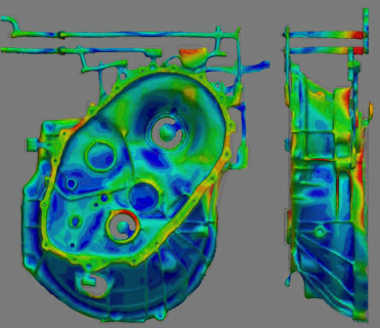
Distortion in HPDC Part
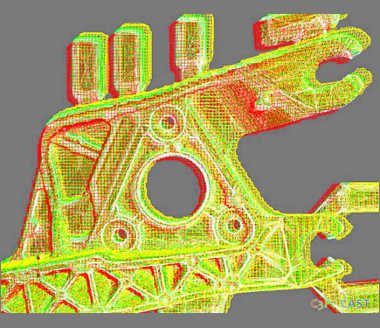
Compensation shape vs Actual design
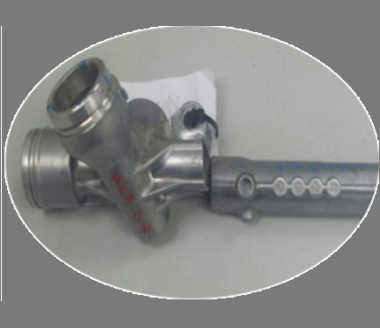
Actual part failed at same location
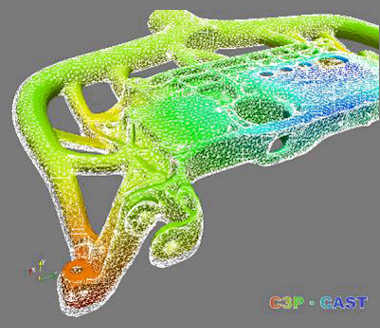
Distortion in LDPC Part
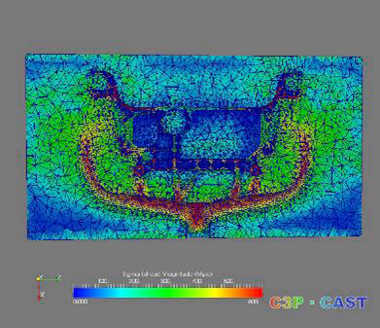