Automatic Optimization
"Artificial Intelligence" a multi-criteria non-linear optimization which is based on Genetic Algorithm and can be executed by Cast-Designer optimizer.
- Multiple Criteria Targets: All physical problems, namely the flow, thermal, stress, war page, micro structure, material properties etc., could be optimized. For Example: Single or multiple targets of the simulation. The foundry engineer is trying to achieve maximize the yield, minimize shrinkage or minimize gas entrapment and balance the flow during the filling process.
- Multiple Design or Process Variable: Design elements that are allowed to vary, could be the Parametric CAD Geometries like runner dimensions, inner gate locations or riser diameter, even original casting part or process parameters like pouring temperature, velocity or the HTC.
- The Genetic Algorithm in Cast-Designer Optimizer checks the result of each optimization iteration like shrinkage, porosity & volume and then intelligently sets the new value of the design variables like size and location for the riser. Such iterations are continued until the targets are achieved.
- Complex user formulas are supported.
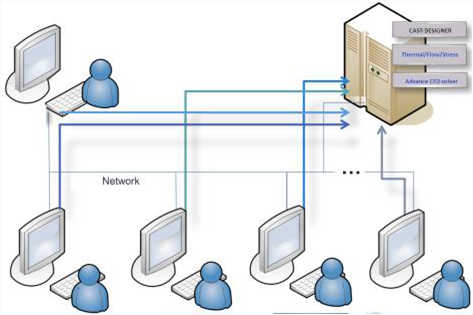
Cast-Designer Optimization supports parallel automatic optimization, this is a breakthrough technology to reduce the lead time of optimization.

DESIGN OF EXPERIMENTS
The Design of Experiment is used to study a process window and its robustness to obtain a set of ideal parameters which provide good result in a user defined goal.
For Example:
- Yield: To find best location and size of risers in order to minimize shrinkage porosity.
- Sensitivity: To identify the sensitivity of the influential process parameters like increasing mould temperature vs. adding an insulation sleeve.
- Cost: Compare costs for maintaining higher melt temperatures vs. rejection/production losses.
- Feasibility: Determine the optimization goals, manufacturing aspects during production and in-line with the known production constraints of a foundry.
PROCESS ROBUSTNESS
Stochastic approach to check that the given process is robust.
For Example:
Vary the furnace temperature within the known range to check that the process is robust. Then find out the maximum and minimum variations that allowed in the process while obtaining the desired good quality parts.
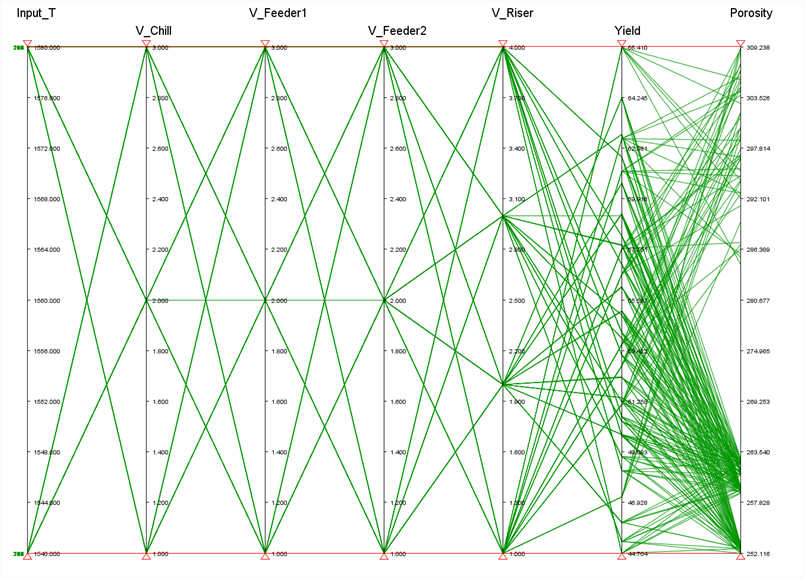
The Taguchi DOE method provides best possible combination of variations. For Example: out of 512 combinations, it is possible to get desired results by trying 16 combinations
HPDC: RUNNER OPTIMIZATION
ORIGINAL DESIGN
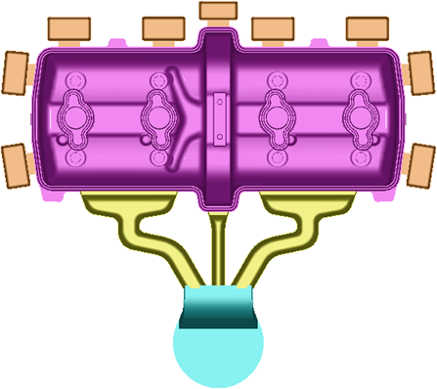
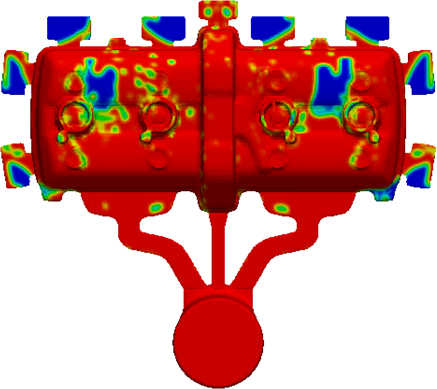
Air Entrapment in filling
OPTIMIZATION SETUP
To achieve air entrapment free flow:
- Optimize the section area factor of the main runner/main gate and sub-runner 1 (SR1) and sub-runner 2 (SR2).
- We set a factor K, if K<1 then the section area SR1 and SR2 will be zero. Also, K will adjust the inner gate area C and D directly.
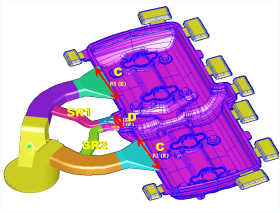
OPTIMIZED DESIGN
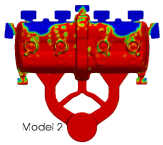
With Optional Sub-runner
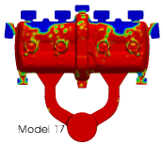
W/O Optional Sub-runner
GRAVITY CASTING: RISER OPTIMIZATION
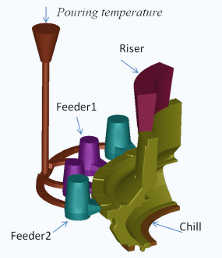
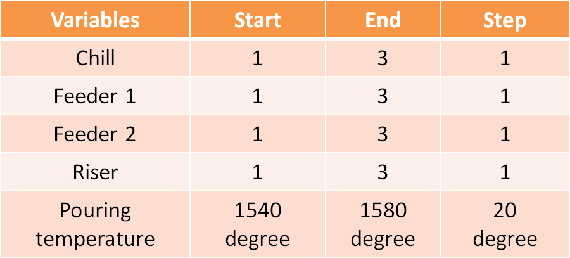
OPTIMIZATION SETUP
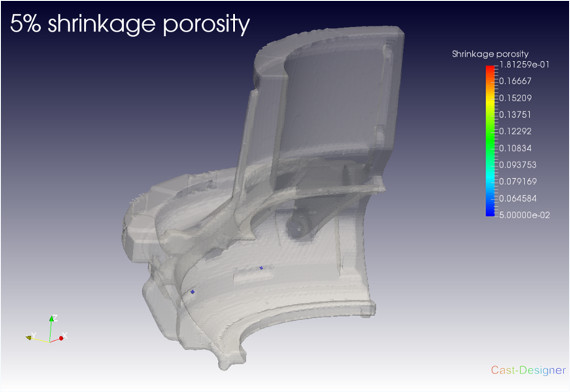
OPTIMIZED DESIGN (The best one)
Casting yield: 59.3%
Shrinkage porosity volume: 253.3
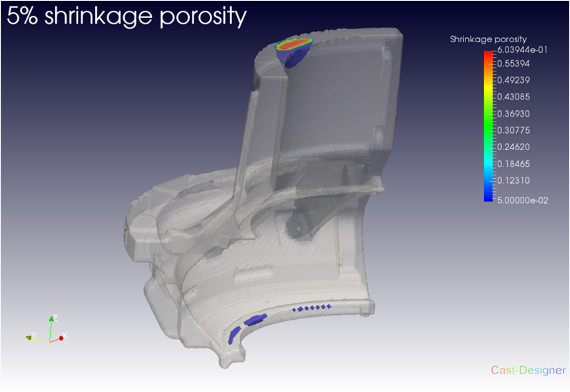
OPTIMIZED DESIGN (The worst porosity)
Casting yield: 56.1%
Shrinkage porosity volume: 287.1
Full combine models: 243 models
Taguchi DOE method: 27 models
User defined condition could be applied to above two methods.
Setup the basic simulation model in 30 min and 1 hour for optimization setup. The 27 runs token 3 hours in 5 token parallel optimization in 20 core Intel E5 machine.
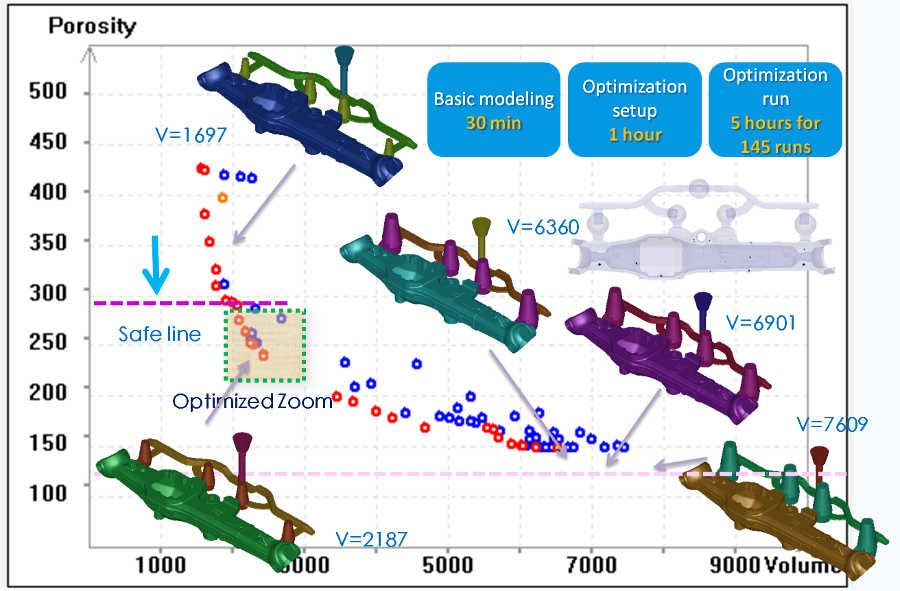
To optimize the casting yield ratio and shrinkage porosity of an automotive part. Using the GA method to find the Pareto front points. The X axis was the total riser volume and the Y axis was the shrinkage porosity volume.
BENEFITS
Cast-Designer Optimizer enables lower research expenditures and decrease implementation time. The main purpose of the system is to relieve a designer or a researcher from the sufficiently complex and very labor-intensive process of searching for the optimal system design parameters which simultaneously meet a great number controversial requirement.