AI-FORM STRETCH FORMING
Design & Simulation Software for Skin Part Forming
AI-Form Stretch Forming (AISF) is a whole package to combine the CAD design, kinematic process design and FEM simulation together to serve the stretch forming process.
AISF using the latest numerical simulation technology and taking into account the real behavior of the blank sheet deformation, with high accuracy as well as faster simulation.
AISF works in two stages of simulation: the kinematic process simulation and finite element simulation to design stretch forming process and create the part program.
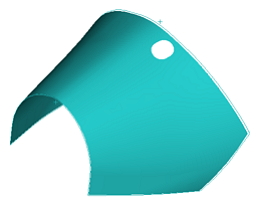
Geometry process
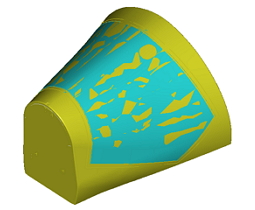
Die design
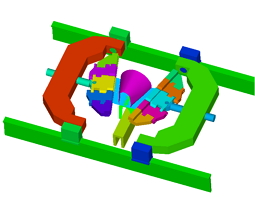
Kinematic Processing
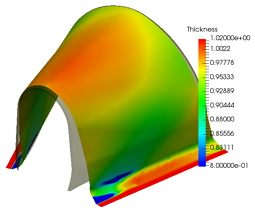
FEM Simulation
AISF MAIN FEATURES & APPLICATIONS
Process Design
- Support all kind stretch forming process, such as transversal wrap, transversal bullnose and longitudinal stretch.
- Build in database with the common VTL series stretch forming machine, also accept the user's defined machine.
- Flexible jaw design function. The jaw's number, location, width and gap could be customized.
- Based on the part geometry, build-in wizard to design the curvature angle of jaws.
- Powerful process management function. All sub-processes are managed in one table, easy to sort the sequence and modify the parameters. Pre-defined templates for difference process.
- Build in tools to predict the kinematics trajectory as the part geometry and given total plastic strain as well as the strain distribution of each sub-process.
- Build in heat treatment wizard, guide the user to separate the stretch forming runs as the maximum plastic strain and define the heat treatment process.
FEM Simulation
- Simulating the stretch forming processes, taking into account the kinematics of the machine to save cost and time on the 'trial and error'.
- Predicting the technological failures of the forming process, such as rupture, wrinkles, orange peel and springback etc.
- Check part feasibility on a given machine.
- Optimizing stretching parameters in order to minimize the sheet sizes, build-in inverse solver for blank sheet flatting.
- Checking part balancing on the machine, and support the die design.
- Create and optimize the trajectory movement of all moving axis according to the deformation required on the sheet to improve part quality.
- Support advance contact calculation for the translation and rotation contact surface, support physical Jaw simulation.
- Support heat treatment process design and simulation.
- Parallel computing to save CPU time.
CAM & Engineering Report
- Generate engineering report based on the machine data and designed process parameters automatically, support multi-language as well.
- Generate a part program which control all kinematic axes of the machine.
- Generate NC programs for CNC of the given stretch forming machine.
User Benefits
- Increases repeatability & part quality
- Enables complex part forming
- Optimizes industrialization time
- Improves productivity and cost structure
- Enhance engineering knowledge of stretch forming.
- Easy to use software and short learning curve.
Virtual Machine
Thanks to the machine database, a virtual machine is available in any time. It could be used for sub-process design and the device motion check.
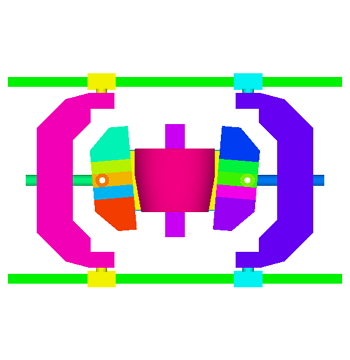
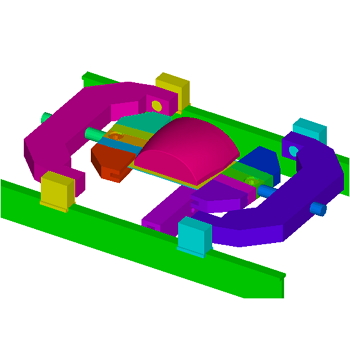
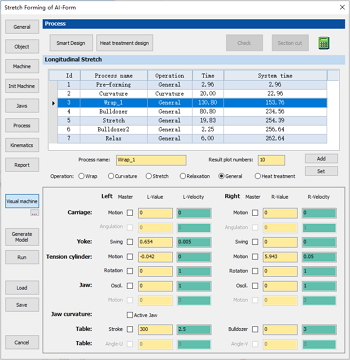
SALIENT FEATURES
- High Orientation Development: Special developed for skin stretch forming process with the given style stretch machine.
- Machine Kinematics: Software customized to machine kinematics.
- Virtual Machine: provides the virtual machine during the process design stage as well as result checking.
- User Friendly: Special designed interface for stretch forming, uses industrial language.
- Auto Design: Build in design tools to generate the kinematics trajectory automatically.
Smart Design for Sub-process Design
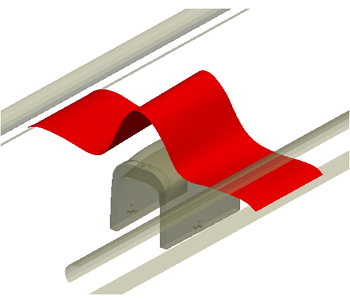
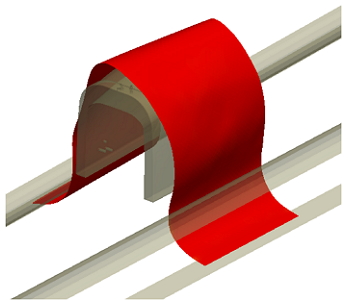
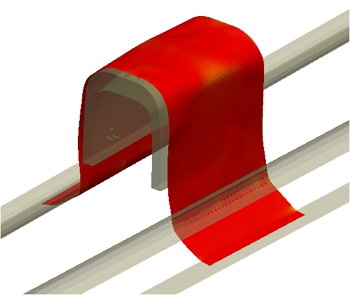
Stretch forming process simulation (Designed by experience)
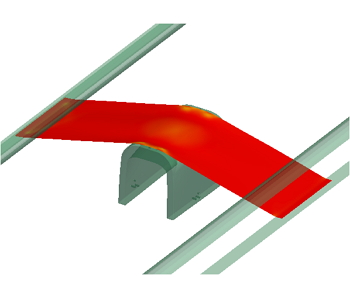
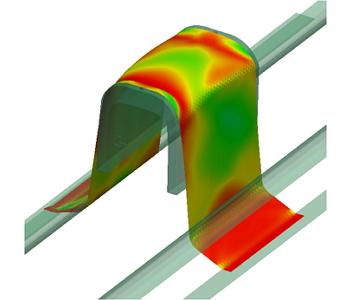
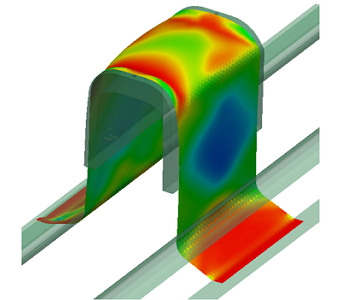
Stretch forming process simulation (Designed by Smart Design)