AI-FORM PEEN FORMING
Peen Forming Process Design & Simulation Software
AI-Form Peen Forming (AIPF) is a software package that focuses on the design and analysis of the peen forming process, combining the design of the peen forming process, forming trajectories and FEM simulation together.
AIPF adopts the latest numerical simulation technology, considering the real mechanical behavior of sheet metal shot peening and comprehensively considering the calculation cost, with high accuracy and efficient simulation speed.
The analysis of AIPF includes two stages: local simulation of the peen process of real shot peening and global FEM simulation of the shot peening process of a large plate, using different analysis models and simulation techniques but in the whole chain.
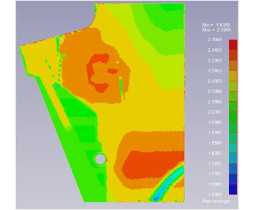
FEM Global Simulation
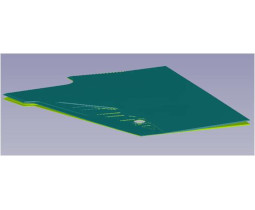
3D blank sheet flatting
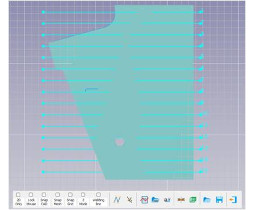
Toolpath Design
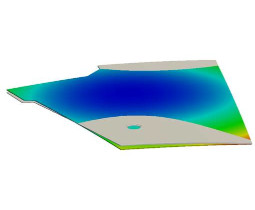
FEM Global Simulation
AIPF MAIN FEATURES & APPLICATIONS
Part analysis and process design
- 3D part unfolding technology, unfold complex 3D parts of non-uniform blank thickness.
- Online tools to check blank thickness.
- Online tools to check part curvature in any direction.
- Analyze the geometric characteristics of the peen part and generate the shot peening strength contour automatically. This contour could be used to design the toolpath of peen forming process.
- Introducing the concept of the peen source value of the peen forming process. The peening process parameters and the strength of the peen source value has been combined together, such as the air pressure, shot nozzle size, nozzle movement speed and coverage ratio are could affect the peen source value.
- A built-in database can provides the peen source value when input the geometry dimension and curvature, this database generated by the neuron network. On the other hand, when the user input the peen source value, the system also can seek the curvature radius of the given dimension thanks to the same database.
- Built-in shot peening toolpath design tool, it can design complex toolpath, and manage different design plans.
FEM Simulation
- Using the latest FEM simulation technology, it can simulate the stress/strain and mechanical deformation behavior of the peening process to save the cost of "trial and error".
- Local simulation model: the dynamic explicit FEM code is used to simulate the local peening forming model, to analyze the effect of different speeds, ball diameters, spraying angles and many other parameters of the peen forming process, the detail stress and strain result as well as the plastic affection region could be analyzed.
- Global simulation model: using the multi-step implicit method to simulate the global peen forming process of the large plate. The global deformation & distortion and stress and strain result could be obtained.
- The affection of shot peening toolpath and peening sequence could be studied.
- The affection of pre-stressing and different boundary condiitons can be taken into account.
- Peening source value is used as the energy input, it is accurate, robust and high computational efficiency.
- Supports parallel computing.
CNC & Engineering Report
- An engineering report is generated based on the process parameters and the used machine data. The report could be used directly in industrial production and supports multiple languages.
- For authorized and specified shot peening machines, the designed process parameters can be converted into NC code directly for the mass production.
Key Value
- Improves the quality and repeatability of shot peening formed parts, especially for complex parts.
- Significantly optimize process quality, reduce process development time and increase productivity.
- Enhanced understanding of the peen forming process.
Key Functions
- Specialized development: The software is "customized" for the peen forming process.
- Dedicated meshing: The system has built-in mesh functionality for surface layer refinement and mesh quality control specifically tailored to the characteristics of shot peening.
- Large forming models: Unique technology allows the design and simulation of shot peening on large forming models with high computational efficiency.
- Industrial language: The software interface is fully industrialized, in industrial language directly.
- Rich design tools: The system has built-in rich design tools, which can quickly design the peen forming toolpath and predict the process parameters.
Peen Source
- The process parameters of the shot peening process are converted into peen source and loaded onto the whole shot peening model for numerical simulation.
- Can consider the process parameters of the peen forming process and directly correspond to the process parameters.
- Based on artificial intelligence database, predict the shot peening results according to the shot peening conditions or predict the shot peening conditions according to the expected results.
- Instant response for easy parameter adjustment.
Local Model Analysis
- The FEM model is automatically generated according to the given parameters.
- Calculations are performed using AI-Form's solver.
- Input parameters can be studied to investigate the sensitivity of the parameters.
- Adaptation to different material models.
- Results are analyzed and extracted.
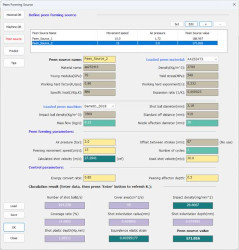
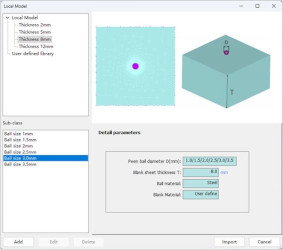
Rich Simulation Results
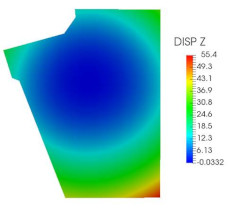
Curvature check
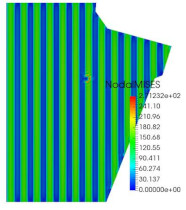
Thickness check

Displacement
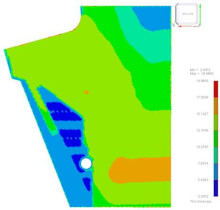
Stress
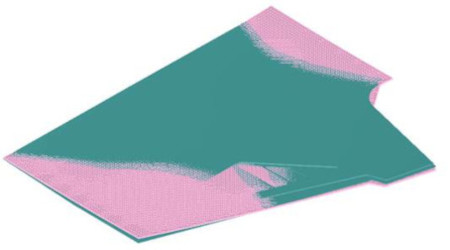
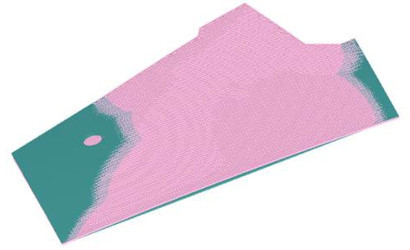
Geometrical comparison of the product after peen forming process (before and after)