Casting-Designer PErformance (CDPE)
Couple the casting result to performance simulation
CDPE stands for (Cast-Designer PErformance) is a software module used for the solution of large-scale, 3-D solid models subjected to static and dynamic loads. The software includes specific features oriented towards the investigation of fatigue and ductile fracture in metals.
CDPE is an analysis engine and fully integrated into Cast-Designer user's environment. The affection of casting defects to the final part performance could be considered well, thanks to the full couple of Cast-Designer solver and CDPE, such as the shrinkage porosity, gas porosity and residual stress.
CDPE MAIN FEATURES & APPLICATIONS
- A library of iso-parametric hexahedron, tetrahedron, interface-cohesive, bar and link elements.
- User-defined multi-point constraints; absolute constraints in global and non-global coordinates; combine with link elements to impose general periodic boundary conditions.
- Tied-contact capability to connect topologically dissimilar but geometrically congruent meshes using automatically constructed multi-point constraints.
- A robust finite strain formulation for solid elements and interface-cohesive elements using rotation neutralized rates.
- The general release of displacement constraints with the relaxation of reaction forces.
- Linear and nonlinear modeling of functionally graded materials.
- Element body forces, face tractions, face pressures, temperatures, piston-theory unsteady face pressures, geometry-dependent face pressures, user-defined nodal-loads routine.
- Displacement extrapolation, line search and automatic, adaptive solution strategies to enhance convergence of global Newton iterations, local constitutive updates and to control growth rates of material damage.
- Contact between the deformable finite element model and a library of rigid surfaces (planes, cylinders, spheres) which may be assigned velocity vectors.
- Full couple casting simulation result to performance simulation.
- Easy to use and short learning curve.
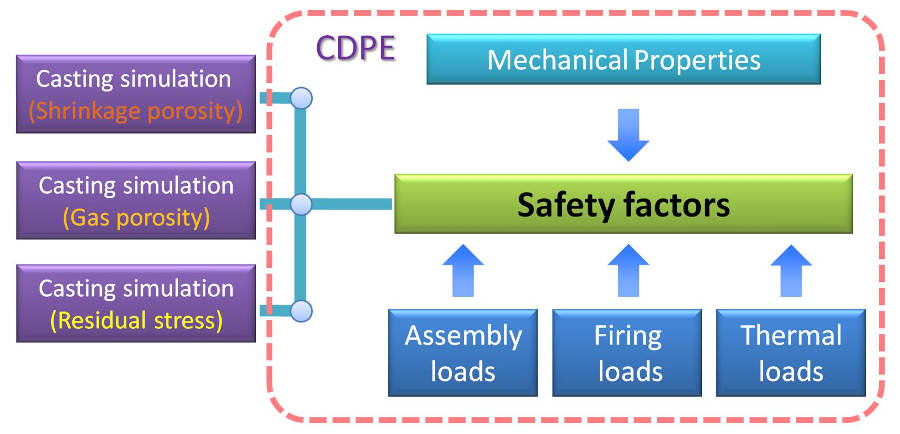
CDPE framework
CDPE: Fully integrated to Cast-Designer system
Same user environment
Same mesh system
Automatic result coupling, no data lose
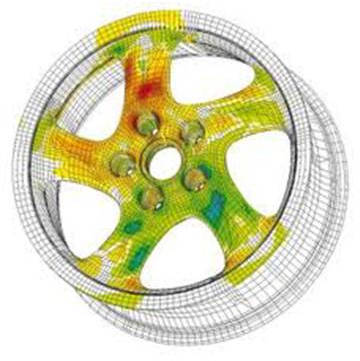
Stress of casting wheel
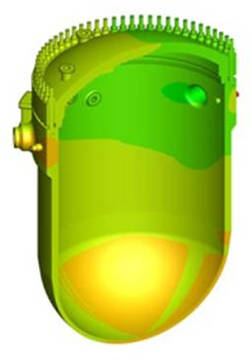
Pressure distribution of CDPE
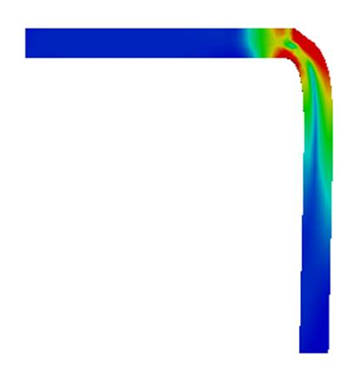
Casting part to consider performance
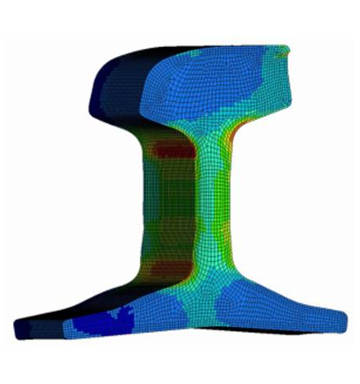
Bending process simulation
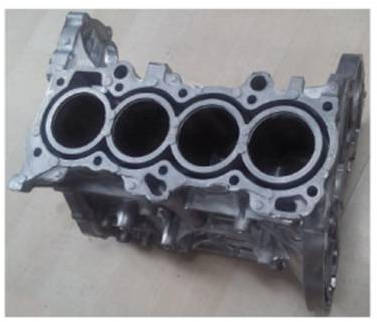
Engine block to consider performance
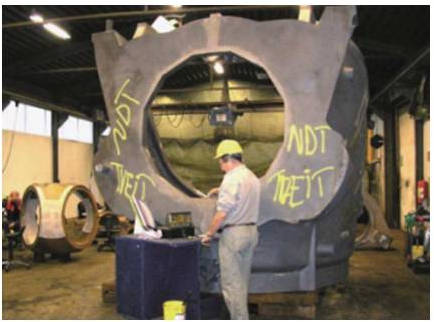
Stress analysis of CDPE
SUCCESS STORY
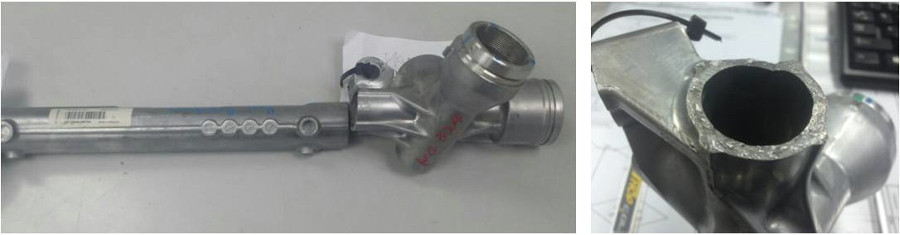
The casting part failed to pass the mechanical testing, but other vendors can pass the testing without problem, so the casting defects is the key of the part performance.
Casting process & defects
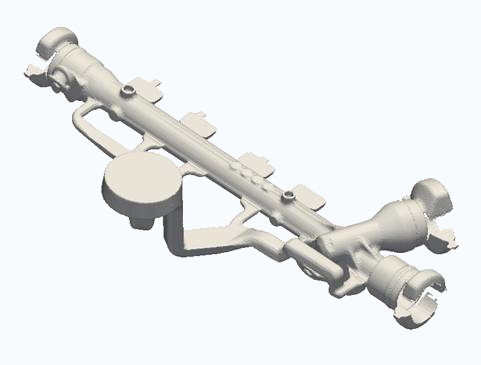
Gating system
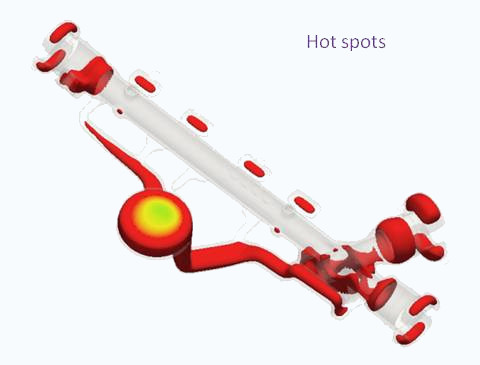
Solidification result
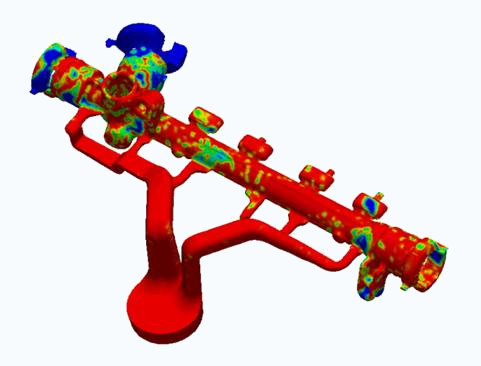
Filling result
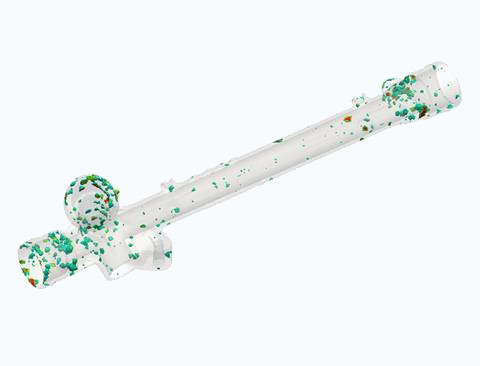
Gas entrapment
CDPE modeling
CDPE executes in a parallel on computers with multiple processors and with multiple cores per processor. The parallel implementation makes use of industry standards: (1) OpenMP for shared memory (threads), (2) Message Passing Interface (MPI) to support a multiple level hierarchy of parallel execution on distributed hardware (clusters) with local parallel execution using shared memory via OpenMP.
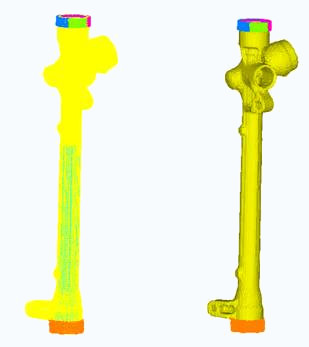
Boundary condition
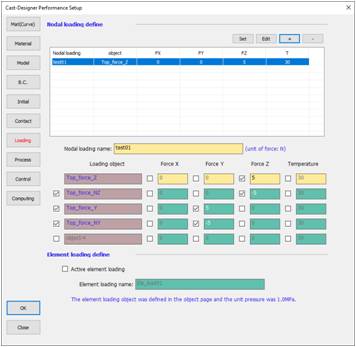
Settings panel
CDPE result
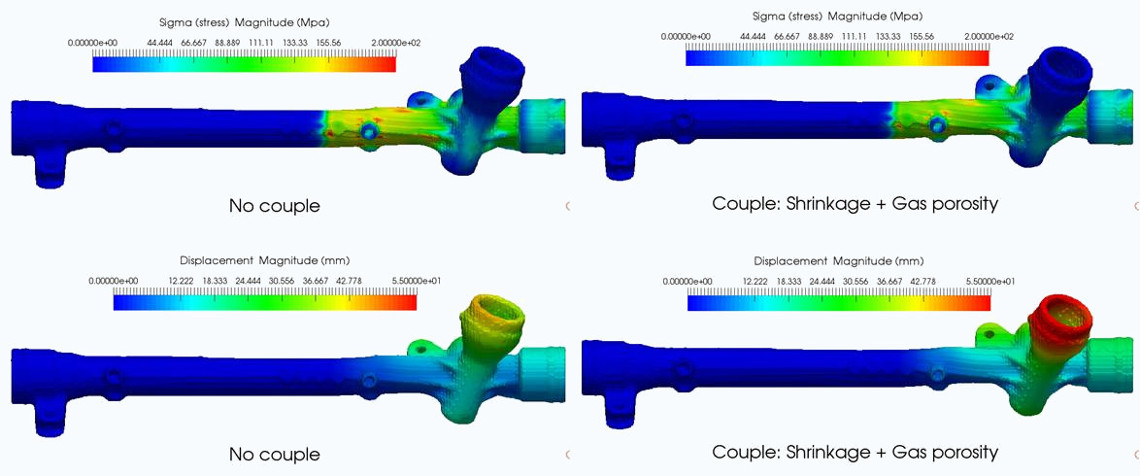
CDPE POWERFUL SOLVER
Support elements: Solids 8, 9, 12, 15, 20 node (hex) isoparametrics; 4, 10 node tets; all with face, temperature, body loadings
Static, impact/dynamic (time-history integration)
Finite-strain plasticity (mises, crystal plasticity, deformation plasticity, hydrogen effects, Gurson-Tvergaard, strain-rate dependent, Frederick-Armstrong & Generalized cyclic, temperature dependent, etc.)
Fully automatic crack growth modelling (element death, CTOA and user controlled node release, interface cohesive, adaptive solution strategies)

Elements model
Solvers: Pardiso (direct, iterative) in Intel Math Kernel Library for threaded parallel execution
Material: incremental Mises with segmental definition of uniaxial true stress-log strain curve. Isotropic hardening. Finite strains.